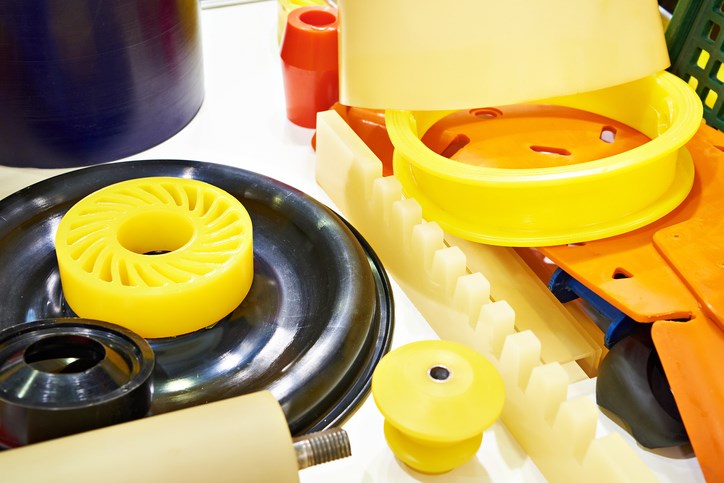
As surprising as it might be to many, injection molding is a process that has been around since the late 1800s. Since then, it has been refined and optimized into the manufacturing process we’re familiar with today. Thanks to its high precision, efficiency in mass production, and ability to create consistent parts on a repeatable basis, injection molding has become a go-to for many businesses’ plastic parts needs. But for businesses that need to take their production a step further, gas-assisted injection molding has emerged as an ideal solution for certain projects. Today, let’s take a look at three plastic parts that are ideal for gas-assisted injection molding (and three that aren’t).
Gas-Assisted Injection Molding: The Process
First, it’s worthwhile to take a closer look at the process of gas-assisted injection molding and what distinguishes it from traditional injection molding methods. Gas-assisted injection molding involves the injection of an inert gas (usually nitrogen) into the mold cavity after the initial injection of molten plastic. The gas displaces the molten material to create channels to hollow and better fill out other sections. This gas pressure is maintained until the part cools in order to ensure the desired shape is maintained.
3 Parts That Are Ideal Gas-Assisted Injection Molding
Large and Thick-Walled Parts
Because of the way the process works, gas-assisted injection molding is incredibly effective at producing large, thick-walled parts without adding a lot of weight. By pushing the molten material through the mold and creating hollows, you can achieve a part that has thick walls without big areas of solid plastic in other areas.
Gas-assisted injection molding also helps mitigate the formation of sink marks, which are a common problem in large, thick-walled parts. But since gas-assisted injection molding facilitates a more even cooling process, sink marks are much less likely. As a result, good candidates for gas-assisted injection molding include automotive panels and structural components.
Hollow and Complex Parts
As has been mentioned above, gas-assisted injection molding is ideal if you need parts created with hollow cavities–but it’s also an excellent choice for complex parts in general. Parts with intricate designs, complex geometries, and internal cavities present challenges to traditional injection molding.
But with gas-assisted injection molding, your manufacturer can ensure the molten material is where it needs to be within the mold. The process also accommodates the creation of undercuts, internal design features, and complex shapes that you might struggle to create with traditional injection molding. Examples of these kinds of parts include handles, enclosures, and housings for electronics.
Aesthetic and Seamless Parts
Finally, if your part requires attractive aesthetics and seamless construction (like many consumer products, for example), gas-assisted injection molding offers a variety of advantages. Gas-assisted injection molding promotes a smooth and high-quality surface finish and helps minimize or even eliminate weld lines.
Gas-assisted injection molding also reduces the need for extensive post-processing. Not only can this save on production costs, but it also means you can achieve a smooth, seamless look for a part that looks continuous. Parts that benefit from this include consumer electronics and medical equipment housings.
3 Parts That Are Not Well-Suited for Gas-Injection Molding
Small and Simple Parts
While gas-assisted injection molding does come with a long list of benefits, there are times when the added complexity of the process may not justify the result. For instance, small and simple parts that are straightforward to produce would not require the additional capabilities of gas-assisted injection molding. As a result, the initial investment for the additional set-up and tooling likely won’t provide enough of a pay-off in terms of product quality.
Parts That Require High Precision
Gas-assisted may not be the best choice for parts that require extremely tight tolerances, either. While gas-assisted injection molding is great for meeting complexity requirements, it does have some limitations in terms of control. Meeting the precision requirements of some parts would require effectively channeling the gas inside the mold, something that is likely easier with traditional methods.
Thin-Walled Parts
Finally, because gas-assisted injection molding relies on controlled expansion of the polymer inside the mold, it is not an ideal solution for parts with thin walls. For one thing, achieving uniform gas penetration in thin-walled sections can be challenging. Failure to do so may result in incomplete fills or uneven thickness, both of which can lead to parts that lack structural integrity.
Experience the Benefits of Gas-Assisted Injection Molding with Thogus
At Thogus, we’re proud to provide mid- to high-volume traditional injection molding, two-shot molding, and gas-assisted injection molding to all of our customers. Our team of highly skilled engineers can help you determine which process would work best for your product. And beyond that, we offer secondary operations and tooling, all delivered with the highest level of white-glove customer service so we can be certain of meeting your every need.
Ready to get started? Contact our team of experts today.
Experience the Thogus Difference
Connect with us today to discuss your project and to learn more about our capabilities.