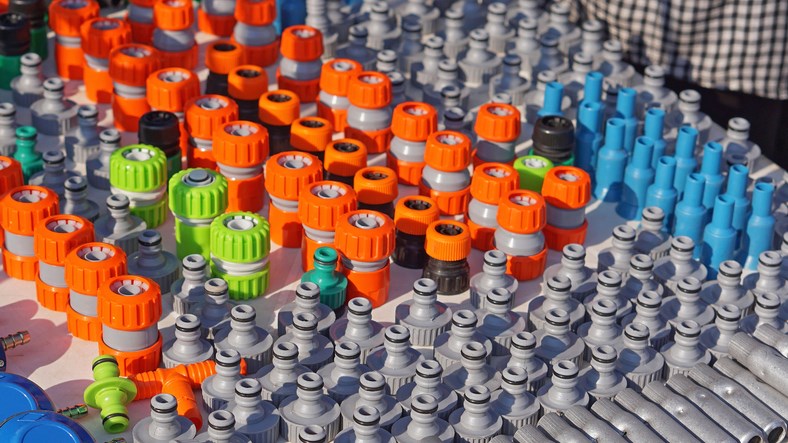
Injection molding has become one of the most popular methods for manufacturing high quality plastic components. There are several reasons for that. It’s a highly precise method that enables manufacturers to produce large quantities of identical plastic parts. It’s also relatively fast, reliable, and cost-effective (particularly for high volume orders) when compared to other plastic manufacturing processes. However, as precise as it is, injection molding is not impervious to producing parts with defects now and again. Sink marks in injection molding, as well as other issues, crop up in many production runs. Fortunately, there are a number of things that injection molders do to avoid or minimize sink marks and other plastic part defects.
The Most Common Defects in Injection Molding
Injecting molten thermoplastics into a mold cavity is bound to come with some challenges. Injection molding is a precise manufacturing process, but that precision also means there is room for error if even one part of the process is off. That, in general, is what leads to some of these common defects:
- Sink marks in injection molding are one of the most common defects. They are depressions or dimples on the surface of a molded part caused by localized shrinkage during cooling. Contributing factors include inadequate cooling time or uneven cooling within the mold, insufficient packing pressure, thick sections in the part design, and excessive injection speed.
- Warping refers to the distortion or bending of a molded part from its intended shape, often resulting in uneven dimensions or curvature. Warping is typically caused by non-uniform cooling of the part within the mold, residual stress in the molded part due to improper mold design, incorrect injection or holding pressure, and improper gate location.
- Short shots occur when the mold cavity is not completely filled during the injection molding process, resulting in incomplete parts with missing sections or features. Common causes include insufficient melt temperature, inadequate injection pressure or speed, improper venting in the mold, and insufficient shot size.
- Burn marks are dark or discolored areas on the surface of a molded part caused by overheating or thermal degradation of the polymer. Excessive melt temperature, inadequate cooling, poor venting, and contaminants in the material or mold are common reasons for burn marks.
- Jetting occurs when the molten polymer shoots or “jets” into the mold cavity with high velocity, leaving behind streaks or lines on the finished part. Jetting is usually caused by narrow or restrictive gate design, high melt viscosity, insufficient mold temperature, and improper runner and gate geometry.
- Knit lines are visible seams or lines on the surface of a molded part or where two more mold flow fronts meet and fuse together during injection molding. Causes include inadequate material flow, complex part geometry, insufficient gate size, and low mold temperature.
How Manufacturers Avoid Defects Like Sink Marks in Injection Molding
Again, while defects like sink marks in injection molding aren’t avoidable altogether, there are several steps that injection molders can take to minimize them or troubleshoot for them before full-scale production begins.
Mold Optimization
By optimizing the mold design for efficient cooling and adequate ventilation, injection molders can help ensure uniform cooling rates throughout the part and prevent air entrapment. Both of these are major factors when it comes to preventing defects like sink marks in injection molding.
Gate design and location is also crucial. Optimizing gate size and shape helps ensure proper material flow into the cavity, preventing flow restrictions and pressure drop. It’s also important for injection molders to select the right gate type and location to ensure uniform filling and avoid flow-related defects.
Proper Material Selection
Material selection is one of the most important decisions during the injection molding process. When it comes to prevention of defects like sink marks in injection molding, selecting the right material for a specific part means taking into account factors like melt viscosities, flow rates, and fill properties.
Choosing a material that meets the requirements of the part geometry and mold design helps to minimize flow-related defects, control shrinkage and warpage, and guarantee a proper surface finish.
Controlled Production Parameters
Controlled production parameters, including optimized cooling time and process monitoring and optimization, play crucial roles in minimizing defects in injection molding by ensuring consistent and precise manufacturing conditions. Optimized cooling times help safeguard against warpage and distortion, enhance the surface finish, and minimize other defects like sink marks in injection molding.
Similarly, process monitoring and optimization allows for early identification of defects or deviations, which allows for real-time adjustments to be made to the manufacturing process.
Regular maintenance
Finally, preventative maintenance, mold maintenance, and machine calibration can all help mitigate defects in injection molded products. By ensuring that equipment and tooling is performing as expected, injection molded plastic parts can be mass produced with cause for concern.
And tight quality control measures help keep everything in check. Process monitoring, regular inspection, root cause analysis, and documentation and traceability all allow injection molders to make proactive decisions to mitigate or eliminate defects like sink marks in the injection molding process.
Get Expertly Crafted Plastic Components with Thogus
At Thogus, we specialize in mid- to high-volume injection molding services for a range of industries, including medical, consumer goods, electronics, industrial, plumbing, and automotive. With a commitment to staying at the forefront of the manufacturing industry, we approach every project with a commitment to customizing our processes to meet the needs of our customers and minimize defects in all plastic parts. Whether you need standard shoot and ship plastic parts or more custom components for critical applications, we have the capabilities to deliver.
Connect with us today to get started.
Experience the Thogus Difference
Connect with us today to discuss your project and to learn more about our capabilities.