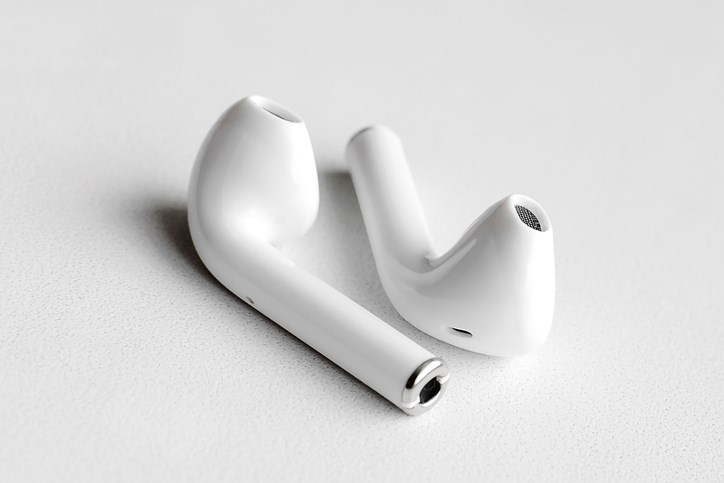
Everything You Need to Know About Manufacturing Plastic Enclosures for Electronics
Find out what goes into manufacturing plastic enclosures for electronics and why injection molding is the go-to method.…
Find out what goes into manufacturing plastic enclosures for electronics and why injection molding is the go-to method.…
Learn everything you need to know about the different types of plastic manufacturing and how injection molding compares.…
Wondering how injection molders achieve high quality in custom molded plastic parts? Find out from the experts at Thogus.…
Is your project right for high volume plastic injection molding? Learn what you need to know from the experts at Thogus.…
Gas-assisted injection molding is an ideal solution for certain parts. Learn more about the process and whether it’s right for you.…
Wondering whether it’s worth it to transfer tooling to a new injection molding partner? Here are 5 signs it might be the right move for you. Learn more.…
The plastics used in medical devices are a special grade of materials that enhance safety and performance. Learn more.…
Two-shot plastic injection molding is a versatile manufacturing method that also delivers a competitive advantage. Learn more.…
Nylon resin is a versatile, high-strength thermoplastic that is well-suited to a variety of injection molding projects. Learn more with Thogus.…
Better part design flexibility is only one advantage of gas assisted injection molding. Learn more with Thogus.…
Overmolding is an excellent solution for simplifying your product’s assembly. Learn more in our overmolding design guide.…
Ever since 3D printing entered the plastic manufacturing scene in the 1980s (much earlier than most people think), it has been rife with potential. In recent years, more sophisticated technology has…