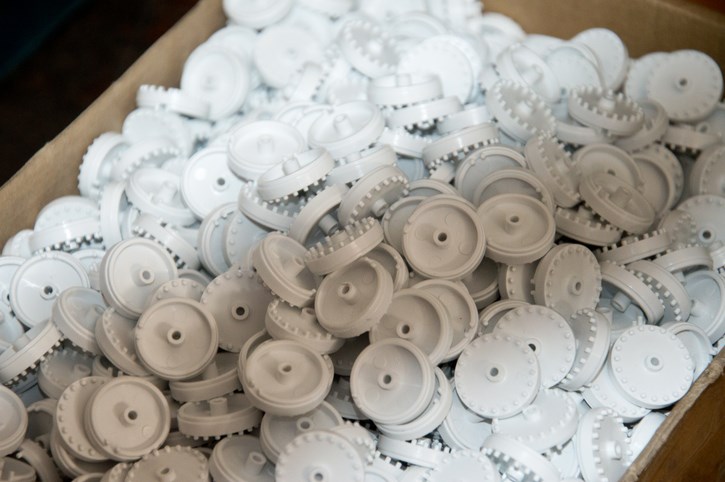
Automotive OEMs operate in one of the most demanding manufacturing environments in the world. Between managing complex supply chains, scaling programs across millions of units, and meeting strict standards for quality, cost, and speed (often all at once), these professionals have a lot on their hands. That’s why so many turn to automotive plastic injection molding solutions.
Fast, precise, and iterative, injection molding is one of the manufacturing methods that is most capable of keeping up with and meeting the demands of the automotive industry. But these capabilities aren’t exclusive to the auto sector.
At Thogus, we see more and more non-automotive OEMs — like those in consumer goods, healthcare, industrial sectors, and beyond — applying automotive-grade thinking to gain a competitive edge. Whether you’re producing 10,000 or 10 million parts, the tools, strategies, and disciplines developed in automotive plastic injection molding can drive real improvements in efficiency, scalability, and product performance.
Let’s take a closer look at how these principles translate beyond the assembly line, and how working with a partner like Thogus can help you build smarter from the start.
Scaling Smart: What Automotive Plastic Injection Molding Teaches Us
One of the most valuable lessons from automotive plastic injection molding is that scale and precision don’t have to be at odds, as long as you plan for them early.
Automotive OEMs know that smart scaling starts long before a part hits the production floor. That’s why they prioritize Design for Manufacturability (DFM) early in the development cycle to align engineering, tooling, and production teams from the start. This approach reduces rework, speeds up validation, and sets the stage for reliable, high-volume output.
Their tooling strategies also reflect a long-term mindset. While high-cavitation, high-precision tools require more upfront investment, they deliver better consistency, lower scrap rates, and faster cycle times over millions of shots. That same logic applies to non-automotive programs expecting growth or tight tolerances. In other words, building for durability pays off.
Finally, the auto industry’s focus on lean production and real-time data allows them to optimize processes continuously. With integrated systems tracking performance, capacity, and quality in real time, they’re able to adapt quickly and minimize downtime. Non-automotive OEMs can apply this same playbook to strengthen operational efficiency and cost control, especially when working with a partner who understands how to implement it.
Driving Efficiency Through Automation
Automation is one of the key pillars of efficiency in automotive plastic injection molding, and its benefits translate far beyond the auto industry.
On high-volume automotive lines, robotics and automation are used to ensure precision, speed, and repeatability while reducing reliance on manual labor. These technologies don’t just increase throughput; they also reduce human error, improve part quality, and help manufacturers meet tight delivery timelines.
At Thogus, we bring that same mindset to industrial, consumer, and medical programs. Whether it’s automated part removal, in-line quality inspection, or robotic packaging, we tailor automation strategies to your part geometry, volume targets, and production goals.
The result? Faster cycles, fewer errors, and production lines that scale without adding headcount. It’s a strategy born in automotive and refined to meet the demands of any high-performance injection molding program.
Quality Control as a Competitive Edge in Automotive Plastic Injection Molding
Few industries demand as much from their suppliers as automotive, and when it comes to quality, there’s zero margin for error.
To meet that bar, the auto sector has relied on some of the most advanced quality systems in manufacturing: APQP (Advanced Product Quality Planning), SPC (Statistical Process Control), and real-time process monitoring, just to name a few. These tools aren’t just for automotive, though — they’ve become valuable benchmarks for any OEM looking to reduce risk and ensure consistency at scale.
At Thogus, we take that same quality-first approach across every industry we serve. Our internal process control system integrates real-time monitoring with production data to detect even minor deviations before they turn into costly scrap or delays. We don’t wait for issues to appear at the end of the line. Instead, we build in quality at every stage.
Supply Chain Resilience and U.S. Manufacturing
The automotive industry has long been a leading advocate for bringing manufacturing back to the United States, and for good reason. Global disruptions, shipping delays, and geopolitical uncertainty have proven just how fragile long-distance supply chains can be (remember the months-long wait times for new cars during COVID?)
That same logic applies across industries. Whether you're producing industrial components, consumer products, or healthcare devices, working with a U.S.-based injection molding partner offers more of a strategic advantage than it has historically.
At Thogus, our Midwest location and vertically integrated model support just-in-time delivery, reduce lead times, and give you more visibility and control. There’s no waiting on overseas shipments or worrying about unexpected tariffs or transit bottlenecks.
And because we manage everything including tooling, injection molding, and secondary operations in-house, we can adapt quickly to changes in demand without compromising on quality or speed.
Bring Automotive Plastic Injection Molding Discipline to Your Product Line with Thogus
At Thogus, we apply the same rigorous standards and advanced strategies used in the automotive industry to help manufacturers across diverse sectors scale their production with precision and efficiency. From design for manufacturability (DFM) to advanced quality control systems, we ensure your projects meet the highest performance and quality benchmarks.
Our expertise spans tooling investment, high-volume injection molding, automation in secondary operations, and supply chain resilience, all backed by our U.S.-based operations and vertically integrated approach. Whether you’re in consumer goods, healthcare, industrial, or any other market, we’re ready to help you leverage automotive-grade strategies to elevate your product line.
Let’s talk about how Thogus can apply automotive-grade strategies to your next injection molding project. Reach out today to explore how we can bring efficiency and scalability to your production while maintaining the quality your brand demands.
Experience the Thogus Difference
Connect with us today to discuss your project and to learn more about our capabilities.