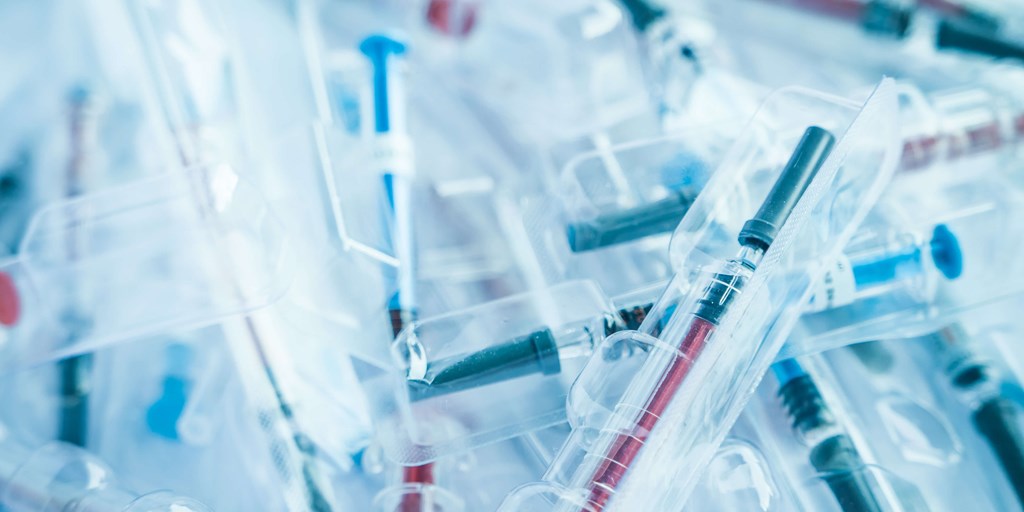
Medical device manufacturing covers a wide range of products used in medical practice, including everything from surgical tools to testing equipment to storage containers for medicines. Regardless of the form, one thing is always true: medical devices exist to keep people healthy, or even to keep people alive, so there is no room for errors or deviations.
In a complex supply chain, errors and deviations can be introduced at any number of stages before ultimately affecting the final product; a fact which the FDA recognizes, as officially the buck stops with product manufacturers when it comes to malfunctioning equipment.
Repeatable Exactness Required
Medical devices are extremely sensitive. Surgical implements require exact specifications in order to operate effectively and must hold up materially under unique stresses. Chemical reactions are also significant risks in medical settings, as reactive polymers can corrupt essential medicines or testing processes. For this reason, medical device products have to be engineered with the end goal in mind from the very beginning, taking into account mechanical design features as well as material selection processes to design the optimal piece for each unique situation.
These manufacturing details and processes are subject to substantial scrutiny by the FDA, who look for issues regarding material ingredients and their proportions, manufacturing processes, mechanical performance of each part, biocompatibility, and toxicity of the materials. Each device must pass this rigorous scrutiny in order to be used safely and effectively.
Once a device is approved, the manufacturing process and material design must be repeated precisely for each individual part to avoid introducing new complications or interactions through accidental deviation.
This is the reason that plastic injection molding is so well-suited to medical device manufacturing — the injection molding process is very robust and repeatable; it ensures a consistent product run after run month after month, year after year, and is capable of producing large quantities of perfectly identical parts.
Plastic Performance
Plastic injection molding also has another unique advantage for medical device manufacturing, and that is the plastics themselves. Plastic resins are both versatile and extremely customizable, meaning they can be designed to eliminate the possibility of interactions with chemicals, like the ones you’d find in hospitals, or in medicines stored in bottles.
They can also be designed to withstand the harsh environments of medical use scenarios, and can pull double weight with regard to functionality. For example, some resins, such as PolyTungsten, can be designed with densities equivalent to lead to create more customizable radiation shielding & radiation focusing parts that are approved by RoHS. Others can be designed to withstand extreme temperatures, consistent moisture, or other environmental factors without affecting product performance.
Regardless of your unique product needs, if you want to take advantage of the safety affordances of plastic injection molded medical device parts, you have to start thinking about design early. Parts have to be designed with the injection molding process in mind in order to select appropriate materials and mitigate the potential for damages or deviations during production.
At Thogus, our manufacturing by design™ process lets you consult with experts who know how to turn your vision for your part into a reality using the best possible design, materials, and manufacturing process. With our years of experience, you can have confidence in a strong design suitable for your application.
Contact us today for a consultation!
Experience the Thogus Difference
Connect with us today to discuss your project and to learn more about our capabilities.