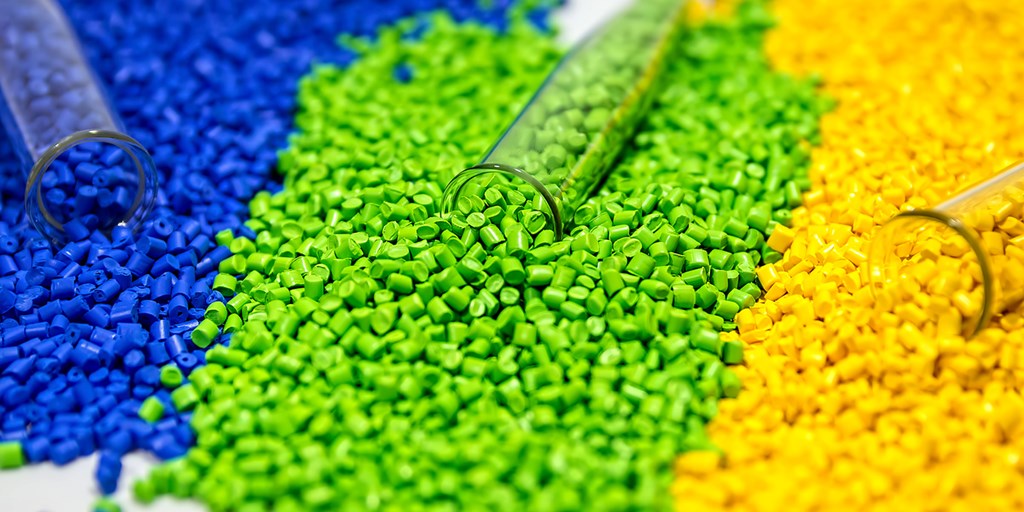
In the past, metal parts have been the default for many manufacturing needs, but with technology advances, more and more manufacturers are deciding to replace metal parts with plastic thanks to the many benefits it can offer. Here are the top 5 benefits of switching.
Weight Reduction
In recent years, weight reduction, or lightweighting, has ranked among the highest priorities for the aerospace and automotive industries. For these industries, weight reduction leads to improvements and efficiencies like using less fuel, creating more economical and eco-friendly products, and saving costs. Even a 10% reduction in the weight of an automobile can improve the fuel economy of that vehicle by up to 8%; meanwhile, a 20% weight reduction of an aircraft like the Boeing 787 can improve fuel efficiency by up to 12%.
Plastic parts are a practical and economic way to maximize lightweighting in these industries. Heavy metal parts weigh vehicles down, increasing overall weight and driving fuel usage through the roof. Some metals like aluminum have been used in the lightweighting process, but the high porosity of lightweight metals could produce unreliable parts. Composite plastics, however, can be engineered to meet the needs of the environment they will function in, keeping all the benefits of lightweighting while avoiding the risks of certain metals.
From Design Freedom to Part Consolidation
Compared to some metal processes, injection molding can improve design flexibility, which allows designers to minimize the number of parts and manufacturing steps needed to produce a finished product. With modern innovations, designers can use the freedom that plastic injection tooling offers to create a single plastic part that replicates the function of several metal parts. Fewer parts further optimize the weight efficiency of the final product as well as transportation costs.
Cost Reduction
All of these efficiencies translate into cost savings. Mass-produced metal parts can take hundreds of labor hours to mill and process, and time is money. Plastic parts can often be produced quicker and more efficiently as a benefit of faster cycle times.
Lightweight plastic parts can also be transported at reduced cost when compared to heavier metal parts, especially if the number of parts has been reduced thanks to the ability of custom plastic tooling to pull double-duty.
Improved Performance
In many harsh environments, certain metals can lose their properties over time. Corrosion of metal parts is both common and incredibly costly, requiring complex processes to address the issue and prevent massive property loss. However, injection molding provides an opportunity to develop custom-engineered resin to stand up to harsh conditions ranging from saltwater to chemicals to extreme heat and pressure.
Changes in Regulations
Regulations and policies protecting the environment, manufacturing employees, and product end-users are becoming more prominent. Engineered resins for custom injection molding can be designed to comply with EPA regulations by limiting VOC emissions. Plastics can also be used to eliminate potentially harmful metals, such as lead, from public products. Because these plastics are customizable, they perform as well as — or better than — their metal counterparts.
Looking to cut down weight and costs while maintaining exceptional performance? Contact the experts at Thogus to talk about making the switch from metal to plastic.
Experience the Thogus Difference
Connect with us today to discuss your project and to learn more about our capabilities.