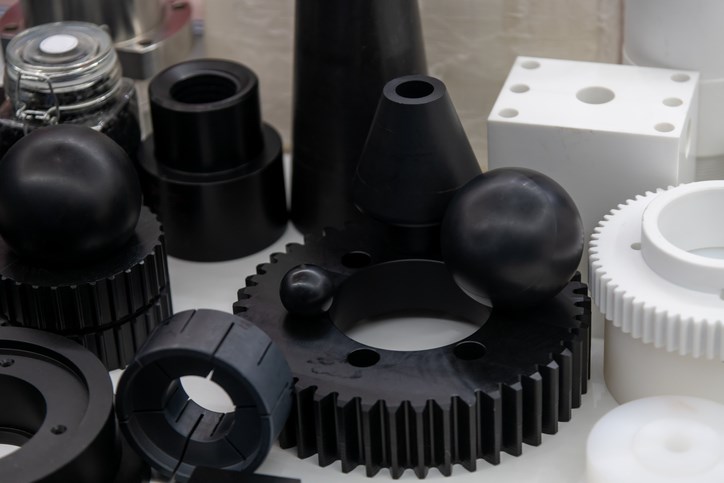
Warping in injection molding is often a symptom of deeper issues in part design, material selection, process parameters, or tooling. When plastic parts cool unevenly or experience internal stress, they can twist or bend out of spec. The result? Parts that don’t function or fail downstream.
For high-volume programs, especially those with tight tolerance requirements, warping can pose a significant risk to product performance, production timelines, and your bottom line. That’s why prevention matters as much as diagnosis.
At Thogus, we bring a problem-solving mindset to every project, and warping is a challenge we engineer around from day one. Whether it’s collaborating early on part design, recommending alternative materials, or fine-tuning process parameters with real-time data, our goal is the same: help customers launch products with confidence and keep them running consistently.
With that in mind, let’s take a closer look at what causes warping in injection molding, and how to stay ahead of it.
What Causes Warping in Injection Molding?
Warping in injection molding doesn’t usually happen by accident. Instead, it’s the result of a complex interplay between part design, material behavior, tooling, and process variables. Understanding the root causes is the first step to solving it. Here are a few of them:
- Uneven cooling rates are a common culprit. When different areas of a part cool at different speeds, internal stress builds up and pulls the part out of shape.
- Material choice matters, too. Resins with high shrinkage rates or directional fiber orientation — especially in filled materials — can distort if not properly accounted for.
- Mold design flaws like improper gating, inadequate venting, or inconsistent wall thicknesses can exacerbate stress concentrations and cooling imbalances.
- Process parameters such as pack/hold pressure, fill speed, and cooling time all affect how the material flows and solidifies — and whether it does so uniformly.
- Environmental factors also play a role. Moisture in hygroscopic materials like nylon can create internal steam pockets that cause unexpected movement or distortion.
Most importantly, warping issues often begin well before the first shot is molded, usually at the design stage.
That’s why, at Thogus, our team works directly with your engineers to flag design risks, recommend geometry changes, and simulate flow behavior before you’re locked into tooling. The result: fewer surprises, fewer change orders, and parts that run as expected from day one.
How to Prevent Warping: Proven Solutions
Warping in injection molding can’t always be corrected after the fact, so prevention is essential. For OEMs managing complex assemblies and tight tolerances, small distortions can compromise fit, performance, and product integrity. That’s why the most effective prevention strategies begin upstream.
Start with Smart Design
A well-designed part is the foundation of warp-free molding. Features like uniform wall thickness, consistent draft angles, and properly placed gates help minimize internal stress and ensure even cooling. Incorporating design-for-manufacturability (DFM) principles early reduces the risk of deformation, especially in geometries prone to imbalance or shrinkage.
Select the Right Material
Different thermoplastics behave in different ways as they cool. Some, like amorphous materials, offer dimensional stability, while others, particularly fiber-filled resins, can warp depending on flow orientation. Matching resin properties to part requirements is critical, especially for load-bearing or assembly-critical components.
Validate with Simulation
Mold flow analysis can reveal stress points, fill patterns, and cooling dynamics before tooling is built. These simulations provide valuable foresight into how a part might warp and where to intervene, whether by adjusting gate placement, cooling channels, or wall structure.
Dial In the Process
Even with a sound design and tool, processing parameters can make or break consistency. Controlling pack and hold pressures, fill speed, mold temperatures, and cycle times helps ensure predictable outcomes. Many warping issues stem from subtle deviations, which is why ongoing monitoring and control are critical.
How Thogus Diagnoses and Solves Warping — Before It Delays Your Program
At Thogus, warping is an engineering challenge we’re committed to preventing from day one. Our process is built around early collaboration, advanced diagnostics, and continuous improvement, all designed to keep your program on track and your parts in spec.
Every new program starts with a detailed review by our engineering team, who evaluate part geometry, material options, and performance requirements with warping risk in mind. From there, we use mold flow simulations to model fill behavior and identify any stress or cooling imbalance before we enter production. This proactive approach reduces tooling rework and shortens timelines.
Once tools are in production, we also use real-time process monitoring to maintain stability across every run. Our presses are tightly controlled for pressure, temperature, and cycle consistency, and any variation is flagged and addressed quickly. If a part shows signs of deformation during sampling or production, we loop in our customers immediately to adjust the process or implement design changes. That responsiveness can be the difference between a minor issue and a missed shipment.
Even after a program is running smoothly, we stay engaged. Our team continues to fine-tune processes and implement improvements that reduce variability and optimize cycle efficiency. For high-volume, high-expectation molding programs, that kind of vigilance is how we deliver reliable parts, again and again.
Don’t Let Warping Throw Your Program Off Course. Turn to Thogus for Your Injection Molding Needs
Warping in injection molding may be common, but that doesn’t make it inevitable. With the right expertise and tools, it’s a challenge that can be anticipated, mitigated, and often eliminated altogether, long before production ever starts.
At Thogus, we bring a proactive mindset to every project. Our combination of engineering collaboration, advanced simulation, and tightly controlled processes helps reduce variability and maintain consistency, even across complex geometries and high-volume programs. Whether you’re launching a new part or troubleshooting warping on an existing tool, we work alongside your team to solve problems early and deliver the results your end product depends on.
Have a challenging geometry or recurring warping issues? Let’s talk through it — Thogus can help.
Experience the Thogus Difference
Connect with us today to discuss your project and to learn more about our capabilities.