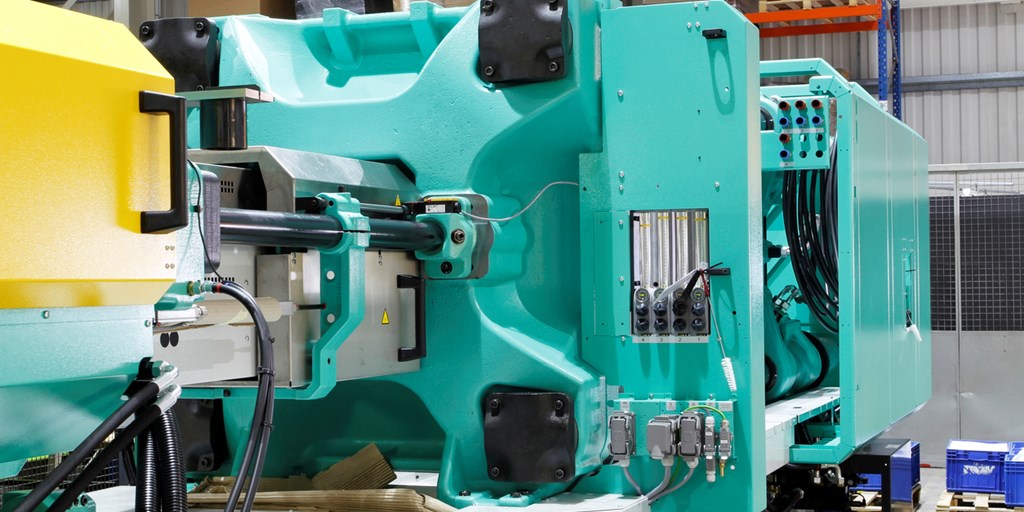
Injection molding can be a cost-effective solution for your parts manufacturing needs. Many manufacturers turn to injection molding, especially at high volumes, because it allows them to produce large quantities of parts in a short timeframe, keeping costs low and programs on schedule. Not all plastic injection molding programs are equal in terms of cost, though. Here are some things you can do to make sure you get the most bang for your buck.
1. Ensure your part is designed specifically for injection molding.
Many industrial parts designers are not experts in plastics manufacturing; their priorities are the look, feel, and function of the product, not the manufacturing process. While the end goal of a product is always top of mind, adjustments to things like wall thickness, draft, and ribbing to optimize a part for the plastic injection molding process can reduce cycle times and lower scrap rates, saving money in the process.
2. Identify the right material that provides the most value.
For any program, it’s important to find the material that has the lowest cost while still satisfying the program requirements. Unfortunately, this step tends to be overlooked. Often, designers pick materials simply because they are familiar (think: “this is the material we’ve always used for this part”) without taking the time to think through all the program requirements and make a choice based on the best available option. Using the right plastic resin for the part function, specifications, and environment can save time and money in addition to improving performance.
3. Understand the importance of ROI when investing in tooling
Sometimes manufacturers don’t want to spend a lot of money on tooling at the start of a project, so they build a cheap tool or a single-cavity tool. Cheap tooling that isn’t optimized for the part and process can result in higher scrap rates, costing more money in the long run. Single-cavity tools are also a tempting, less expensive option at the beginning of a project. But increased cavitation tools, while more expensive to design and build, reduce the overhead cost per part. That’s because they let you create more parts, faster, reducing the overhead hourly rate per part and saving more money in the long run.
4. Work with a shop that understands in-process automation
The process of extracting the part from the machine and then indexing that part is crucial to the success of the run. Many manufacturing shops use an operator to facilitate this process, but operators add labor costs as well as time, as the cycle must be shut down and then restarted to allow a human to reach in and extract the part. In-process automation can replace the function of the operator, reducing labor costs and decreasing cycle times, both of which are good for the bottom line.
At Thogus, we value full partnership from the beginning of your manufacturing process to the end. Our manufacturing by design process™ provides feedback to clients to ensure parts are optimally designed for plastic manufacturing.
We work with material suppliers to ensure the right resin is selected that provides the most value, and with our tool makers and clients to ensure the right tool is used for each application. We have the engineering resources, including robotics, automation, and experience with high-volume runs, to minimize costs throughout the manufacturing process.
Contact us to talk through your custom plastic injection molding needs.
Experience the Thogus Difference
Connect with us today to discuss your project and to learn more about our capabilities.