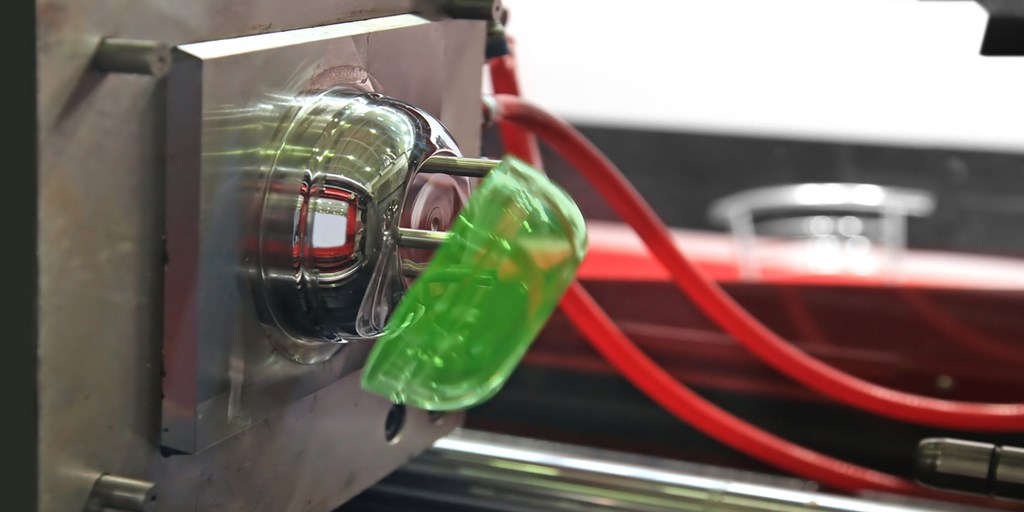
As we always say, successful custom plastic injection molding starts with design. Knowing some key injection molding terminology can help you visualize your part design and communicate it effectively with your injection molding partner. Thogus has experience with a broad range of processes and materials and can provide guidance on the processes and materials that will work best for your project needs.
Commodity Resins
- What they are: Low-cost, standard-performing, but high-volume materials that are easy to process. Contrast with engineered resins.
- When they’re used: Commodity resins are used for high-volume projects when you need to keep costs low and performance requirements are fairly typical. For high-performance needs, it’s worth the price to pay more for an engineered resin.
- Examples: Polypropylene (PP), Polyethylene (PE), High Impact Polystyrene (HIPS), Polyvinyl Chloride (PVC), Acrylonitrile Butadiene Styrene (ABS).
- Note: Commodity resins aren’t well-suited for high-performance products.
Engineered Resins
- What they are: Material designed for specific performance characteristics that tends to be more expensive and higher-performing than commodity resins.
- When they’re used: When specific performance requirements such as heat resistance, conductivity, shielding, or structural strength are required.
- Examples: Glass-Filled Polypropylene (GFPP), Polyethylene Terephthalate (PET), Polybutylene Terephthalate (PBT), Polycarbonate (PC), Polyphenylene Sulfide (PPS)
- Note: The goal is to choose the material that provides the most value in terms of both performance and cost. Thogus experts can help you choose the right materials for your project.
Over Molding
- What it is: Over molding is an umbrella term that describes any process where plastic is molded onto another part, whether that part is plastic or another material.
- When it’s used: Over molding is used whenever a part or product needs to have components with different material qualities.
- Examples: Insert molding and multi-shot molding are both examples of over molding processes.
- Note: Start-up costs in any over molding process can be high, and it’s important to distinguish between insert molding and multi-shot molding from the beginning of your product design.
Insert Molding
- What it is: the process of placing a foreign (usually metal) part in a mold before the mold is filled with plastic; the injected plastic then forms around the interior part, holding it in place within the larger structure.
- When it’s used: This is usually done to add strength to the plastic part, either for overall functionality or as a bolster if another piece needs to be screwed in. Insert molding can also be used to add conductive elements to otherwise non-conductive plastic parts.
- Examples: The blade for a disposable tape dispenser or the riser rod of a crossbow are both insert molded.
- Note: Make sure that the plastic part is designed to receive the insert well. The process of inserting the foreign piece into the mold can also affect the production process; manual insertions take longer than automated inserts. Talk with your supplier to make sure the outcome is exactly what you need.
Multi-Shot Molding
- What it is: A manufacturing process in which multiple materials are molded in a single machine. The substrate is the first piece that is molded, and additional materials are added to that piece. The majority of multi-shot programs are composed of just two materials, so you may also hear this called “two-shot molding,” though larger numbers are possible.
- When it’s used: Any time multiple materials are needed to achieve the desired function or aesthetic of a part.
- Examples: The seal on the plastic lid of a drinking cup or knobs and switches that require covers require multiple shots.
- Note: Multi-shot molding requires more elaborately designed tooling, which can result in high startup costs.
Gas-Assist Injection Molding
- What it is: A molding process in which gas is pumped into the mold during the injection molding process, creating a gap for the plastic to flow around. This decreases the amount of plastic material in the final part.
- When it’s used: This process is used to reduce the material used in a part, either for light-weighting or to create uniform wall thickness.
- Examples: In kitchen appliances, gas-assist injection molding can be used to create hollow handles, or in a small appliance housing to create uniform wall thickness and eliminate sink marks.
- Note: Proper tool design and timing are essential in gas-assist injection molding.
Secondary Processes
Heat Staking
- What it is: Heat staking is the process of using a heated piece of metal to melt plastic, allowing two parts to join together and eliminating the need for over molding.
- When it’s used: Heat staking eliminates the need for multiple fasteners, as all parts can be added in a single process. It also creates very strong bonds.
- Examples: In medical device assembly, heat staking can be used to attach adhesive patches to wearable devices.
- Note: A precise combination of heat and pressure is required for successful heat staking; improper equipment may not be able to maintain these specifications and therefore might damage parts.
Pad Printing
- What it is: Pad printing is a way to apply a printed design to a part.
- When it’s used: Some designs are only aesthetic, meaning they improve the appearance of a part. However, other designs are functional. This allows parts to be customized to suit different situations.
- Examples: Open/close instructions on bottle caps are often pad printed.
Plating
- What it is: Plating is the process of adding a metal coating over a plastic molded part.
- When it’s used: Plating can be used to create a desired aesthetic for a part or to allow a product to perform as intended.
- Examples: Chrome-plated automotive parts are plated.
- Note: Any defects in a plastic part will be much more visible once that part is plated, so be conscious of your tool design. Also make sure to choose a reputable, high-quality supplier and to choose the right resin so the plating will adhere.
Ultrasonic Welding
- What it is: The use of high-frequency ultrasonic vibrations to melt plastic, allowing a part or component to be added in the manufacturing process.
- When it’s used: Ultrasonic welding is used after molding to attach plastics, lightweight metals, or other materials to plastic parts.
- Examples: Automotive door and instrument panels are often ultrasonically welded.
- Note: Ultrasonic welding can cause mechanical damage due to intense vibrations with fragile or crystalline parts. Rounded corners also usually work better for ultrasonic welding than sharp edges, which might crack.
Thogus has the experience and resources to help with all your custom plastic injection molding needs. Contact us to get the conversation started!
Experience the Thogus Difference
Connect with us today to discuss your project and to learn more about our capabilities.