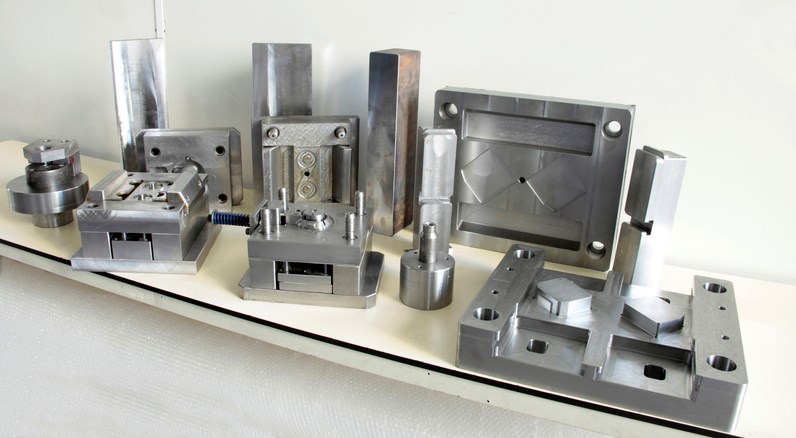
The longevity of injection molding tooling directly impacts production efficiency and cost-effectiveness. That’s why maximizing injection molding tooling life is such a high priority for manufacturers. Longer-lasting tools result in higher levels of precision, repeatability, and long-term performance, especially for high-volume production.
But how do injection molders create tools that last longer? Let’s take a closer look at some of the key factors that influence injection molding tool life and the best practices for keeping molds in peak condition.
Why Injection Molding Tool Life Matters
Over time, repeated cycles, high temperatures, and material abrasiveness contribute to mold degradation. This, in turn, often results in unplanned downtime and costly tool repairs or replacements.
A few key factors that affect mold longevity include:
- Material selection: Highly abrasive resins, glass-filled materials, or corrosive additives accelerate tool wear. Choosing the right mold steel and coatings can help counteract these effects.
- Cycle count and production volume: High-volume manufacturing increases wear over time. Monitoring cycle counts and scheduling preventative maintenance ensures molds remain in top condition.
- Operating conditions: Factors such as temperature control, clamping pressure, and ejection forces all play a role in mold longevity. Optimizing these parameters minimizes unnecessary stress on the tooling.
Proactive maintenance strategies like regular inspections, proper cleaning, and lubrication can help mitigate these risks. By extending the injection molding tooling life span, manufacturers minimize disruptions, lower costs, and enhance the production of consistent, high-quality parts.
Essential Preventative Maintenance Strategies
Routine Cleaning and Inspection
Regular cleaning prevents residue buildup from resins, additives, and gases that can degrade the mold surface. And routine inspections help identify early signs of wear, such as surface pitting, cracks, or alignment issues, allowing for corrective action before they become major problems. Lubrication of moving components, such as slides and ejector pins, also reduces friction and prevents premature wear.
Proper Storage and Handling
When molds are not in use, improper storage can lead to rust and mechanical damage. Molds should be cleaned, dried, and coated with a rust inhibitor before storage. Proper handling — including controlled temperature and humidity conditions — also helps ensure that molds remain in optimal condition between production runs.
Cooling System Maintenance
The efficiency of a mold’s cooling system directly impacts cycle times and part quality. Over time, cooling channels can become clogged with scale, sediment, or corrosion, reducing heat transfer and leading to inconsistent cooling. Routine flushing and cleaning of cooling lines help maintain thermal efficiency, preventing warpage and other defects caused by uneven cooling.
Venting and Gating Optimization
Finally, poor venting and gating can lead to common molding defects like burn marks, excessive flash, and pressure imbalances — all of which contribute to tool wear. Ensuring vents are properly sized and free of blockages allows trapped gases to escape, preventing unnecessary stress on the mold. Gating adjustments can also help optimize material flow and reduce excessive pressure that accelerates mold deterioration.
Advanced Maintenance Techniques for Extended Injection Molding Tool Life
While routine maintenance is essential to extending injection molding tool life, leveraging advanced techniques can further extend the lifespan of injection molds. Some of these strategies include:
- Predictive maintenance with sensors and AI: Traditional maintenance schedules are often based on set intervals, but predictive maintenance takes a more data-driven approach. By integrating sensors and AI-driven monitoring systems, manufacturers can track mold performance in real time. This data helps identify early signs of degradation and allows for proactive intervention before issues cause defects or downtime.
- Refurbishing and recoating: Even with the best maintenance practices, injection molds experience surface wear over time. Refurbishing and recoating techniques can restore mold surfaces and enhance durability. These treatments not only extend mold life but also enhance part consistency by reducing sticking and flow issues.
- Precision machining for repairs: When molds develop surface defects or dimensional inaccuracies, precision machining techniques (e.g. laser welding, CNC machining, etc.) allow for targeted repairs that can restore them to their original specifications.
With these advanced maintenance techniques in place, manufacturers can significantly improve mold longevity, reduce costly downtime, and maintain the highest standards of part quality in high-volume injection molding operations.
Partnering with an Experienced Injection Molder for Long-Term Success
Maximizing injection molding tool life requires expertise, proactive solutions, and a commitment to quality at every stage. Partnering with an experienced injection molder like Thogus ensures that your tooling investment is protected and optimized. Our tooling services and capabilities include:
In-House Tooling Expertise for Proactive Maintenance
At Thogus, we understand that proper mold maintenance is key to production efficiency. Our in-house tooling experts perform routine inspections, preventative maintenance, and rapid repairs to extend tool life and minimize unplanned downtime. With a data-driven approach, we also monitor mold performance, identify early signs of wear, and implement proactive solutions that keep production running smoothly.
Quality-Driven Manufacturing for Longer Tool Life
When you work with an injection molder that prioritizes quality and precision, your tooling lasts longer and produces more consistent parts. At Thogus, we emphasize optimized processing parameters, expert material selection, and controlled molding conditions. By refining our processes, we successfully help clients achieve greater tool longevity while maintaining high-performance production.
Comprehensive Tooling Support: Transfers, Refurbishment and Lifecycle Management
For companies looking to improve their tooling performance, we also offer full tooling lifecycle management, including:
- Tool transfers — Whether transitioning an existing mold from another supplier or optimizing its performance, we ensure a smooth, efficient transfer process.
- Refurbishment and repair services — We restore worn tooling with precision machining, recoating, and surface treatments to extend its usability.
- Lifecycle planning and long-term cost savings — Our team helps customers develop strategic tooling plans to maximize productivity and cost efficiency over time.
By choosing Thogus as your injection molding partner, you gain a team that’s committed to protecting your tooling investment, improving production outcomes, and delivering long-term manufacturing success.
Ready to optimize your injection molding process? Contact us today.
Experience the Thogus Difference
Connect with us today to discuss your project and to learn more about our capabilities.