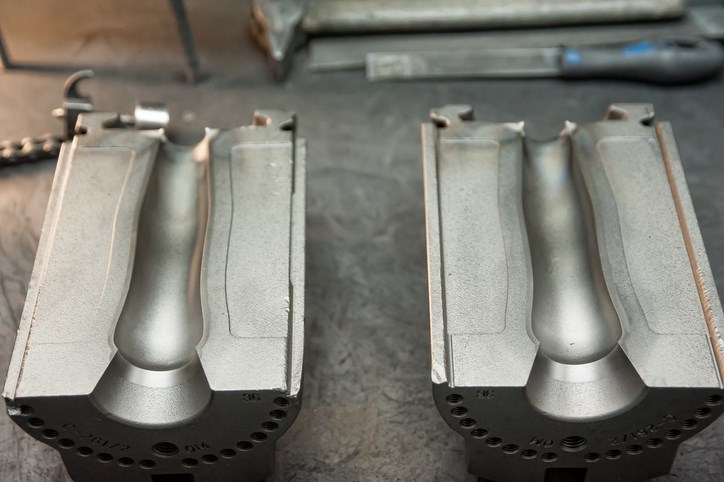
Injection molding tools are often one of the largest upfront investments, and for good reason: they form the foundation of your production program. When tools are properly maintained and strategically upgraded, they enable better parts, fewer disruptions, and more predictable costs.
At Thogus, we take a long-view approach to tooling. Whether you’re launching a new program or scaling an existing one, we partner with you to plan for tool longevity from day one. That means anticipating wear, aligning tool performance with production demand, and identifying upgrade opportunities that reduce downtime and support continuous quality. Because when your tooling strategy is built to grow with you, everything else — from production speed and part quality to cost efficiency and a healthy supply chain — usually follows. Let’s take a closer look at why being strategic with your injection molding tools is the smart move.
The Hidden Costs of Pushing Injection Molding Tools Past Their Prime
When you’re focused on maintaining momentum in your production line, it’s easy to delay tool maintenance or replacement. But the longer this goes on, the more you run the risk of serious consequences. Worn-out tools can lead to degradations that, whether big or small, can ripple through your entire operation.
Part quality begins to slip, for example, leading to increased scrap and costly rework. Cycle times stretch as tools lose their ability to maintain tight tolerances, eating into production efficiency. And when tools fail unexpectedly, you’re not just dealing with emergency repair costs; you’re risking missed deadlines, lost customer trust, and revenue-impacting delays.
Rather than wait for failure to force action, it’s far more cost-effective to plan ahead. Knowing when a tool needs preventative maintenance, reworking, or a full replacement helps avoid these downstream costs and keeps your operation running smoothly.
Key Indicators It’s Time to Rebuild, Refurbish, or Replace
Injection molding tools are built to last — but they’re not built to last forever. Over time, signs of wear become harder to ignore.
You may notice subtle issues first: surface wear that affects part finish, venting problems that lead to short shots or burns, or cooling inefficiencies that throw off cycle times. Dimensional drift is another red flag, especially when it starts to push parts out of spec.
Beyond physical wear, changes in your production demand can also signal the need for action. If your original tool was built for lower volumes but your program has scaled significantly, it may no longer be capable of keeping pace efficiently or reliably.
An increase in unscheduled downtime or frequent maintenance requests is often the tipping point. At that stage, you're spending more to patch the problem than you would to fix it properly. Rebuilding or replacing the tool becomes not just a quality decision, but a cost-control strategy as well.
Strategic Upgrades vs. Reactive Fixes for Injection Molding Tools
Running tooling to failure may seem like a way to squeeze out every last cycle, but it often ends up costing more in the long run. Emergency repairs can halt production unexpectedly, leading to costly downtime, expedited shipping charges, and unhappy customers.
Proactive, planned upgrades offer a better path. Targeted actions like reworking high-wear areas, optimizing cooling channels, or updating components during scheduled downtime can preserve part quality and reduce operational risk without disrupting your supply chain.
At Thogus, we take a lifecycle approach to tooling. Our in-house team conducts regular mold audits and performance assessments, helping you track tool condition over time. We also collaborate with you to plan upgrades in advance — aligned with your production schedule and growth trajectory — so you can stay ahead of wear and avoid last-minute surprises.
Scaling Smart: How Upgraded Tooling Supports Growth
As demand increases, your tooling needs to keep pace. Upgrading or modifying molds is one of the secrets to higher efficiency and performance, both of which support your next stage of growth.
Improvements like enhanced cooling systems, tighter tolerances, or redesigned gating can significantly reduce cycle times and improve consistency at scale. And as you integrate more automation — whether in part handling, quality checks, or downstream assembly — your tooling may need modifications to stay compatible.
At Thogus, we build tooling strategies that grow with your business. Whether you're ramping up from pilot runs to full production or adapting to new automation processes, we engineer with scalability in mind. Our team works closely with yours to ensure tooling upgrades aren’t just reactive, but also intentional, forward-looking, and aligned with your operational goals.
How Thogus Supports Smart Decisions for Injection Molding Tools
Tooling isn’t a one-time investment; it’s a dynamic part of your long-term success. That’s why we Thogus bring deep in-house tooling expertise to every program, helping clients make confident, informed decisions at every stage of the tool’s lifecycle.
Our tooling team works hand-in-hand with engineering and production to evaluate performance, recommend proactive upgrades, and plan for scalability.
Whether you’re managing a domestic tooling transfer, considering a refurbishment, or planning for full replacement, we aim to make the process seamless. With a fully integrated team under one roof, we minimize risk, reduce downtime, and keep production moving.
Future-Proof Your Program with the Right Tooling Partner
Your tooling strategy influences every part you’ll make, every timeline you’ll manage, and every margin you’ll protect. A proactive, scalable approach ensures your tools evolve alongside your program, rather than hold it back.
At Thogus, we help OEMs and product teams stay ahead with tooling solutions built for longevity, flexibility, and performance. Whether you’re scaling up, facing wear and tear, or planning your next program, we’re here to guide you through the right next step.
Let’s make sure your tooling is ready for what’s next. Talk to our team about a tooling assessment or lifecycle plan tailored to your production goals.
Experience the Thogus Difference
Connect with us today to discuss your project and to learn more about our capabilities.