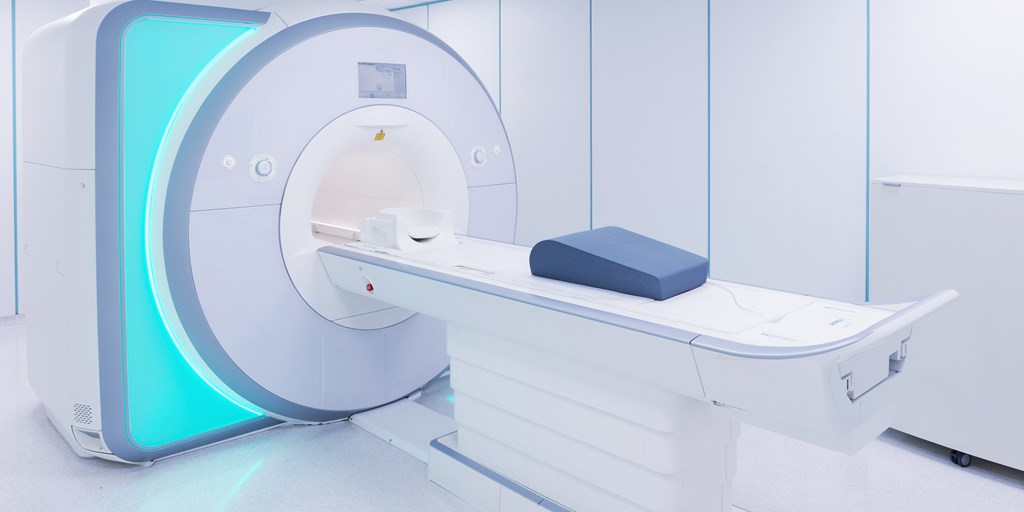
Medical manufacturing is trending away from metals and toward plastic polymers. Part of this trend revolves around the safety benefits of plastics over heavy metals typically used in shielding like lead, which can be harmful to patients. And now, plastics can be engineered to perform under the same circumstances — and to the same quality levels — without the associated risks.
Plastics also offer increased design flexibility when compared with their metal counterparts. They are less visible in an x-ray, are safe, and allow the part to be designed to tighter specifications.
What is Radiation Shielding?
Radiation Shielding safeguards people and equipment from scatter radiation and contaminants that can occur during medical testing and procedures. In the past, lead has been used for most Radiation Shielding because its specific gravity — 11 — is high enough that radiation particles “get lost” as they strike the dense clusters of atoms that make up the heavy metal.
To achieve the same effect, Tungsten-filled nylon with a specific gravity also capable of reaching 11 can be used in the process of plastic injection molding for Radiation Shielding. That means any Radiation Shielding part ordinarily made with lead, from x-ray bibs to CAT scan components, can be made with plastics instead with the same effectiveness but improved safety.
Not all parts require the same degree of shielding, though. It’s important to determine whether part thickness or the intrinsic qualities of the material used to make the part are the focal points. In some cases, a specific gravity of 11 might not be necessary and a less-dense (and therefore less expensive) polymer may suffice.
These factors also affect the design of the part, so the part needs to be designed for proper shielding from the beginning. Final parts should always be tested to ensure they achieve the required goals.
The Solution to the Lead Problem
The use of tungsten-filled polymers can help move away from toxic and harmful lead parts, but of course the safer option isn’t always the least expensive. Many OEMs balk at the price tag when first exploring plastic options over the relatively inexpensive lead. That’s why it’s important to partner with a company with the expertise to develop a cost-efficient strategy for replacing lead with a safer, plastic-based option.
When it comes to making the switch and undertaking this process, material expertise is just as important as the material itself — it’s not something you can take on by yourself.
As a response to the hazards that lead poses in Radiation Shielding, Thogus started a separate unit, Radiation Protection Technologies (RPT), to develop a proprietary combination of tungsten and polymers called PolyTungsten. PolyTungsten shields with the same effectiveness as lead and retains its shape during use better than many other plastic options. It’s safe and reliable, meeting U.S., EPA, OSHA, and RoHS standards.
Injection molding using PolyTungsten is challenging, with few companies able to do it. Many have tried to mold parts for Radiation Shielding and failed because of the challenges associated with working with such a dense polymer, creating costly piles of scrap or overstocking expensive inventory.
Thogus has been a leader in the move from lead to plastic injection molding in Radiation Shielding for more than 10 years. The world’s largest manufacturing companies requiring Radiation Shielding rely on the unique experience offered by Thogus to mold the parts they need using tungsten-filled polymers. This is because Thogus knows what works and what doesn’t from both a tool design and a processing perspective. If you’re considering how tungsten-filled polymers can support your business needs, our expertise can minimize the time and cost needed to do so successfully; talk to us early in the process.
Experience the Thogus Difference
Connect with us today to discuss your project and to learn more about our capabilities.