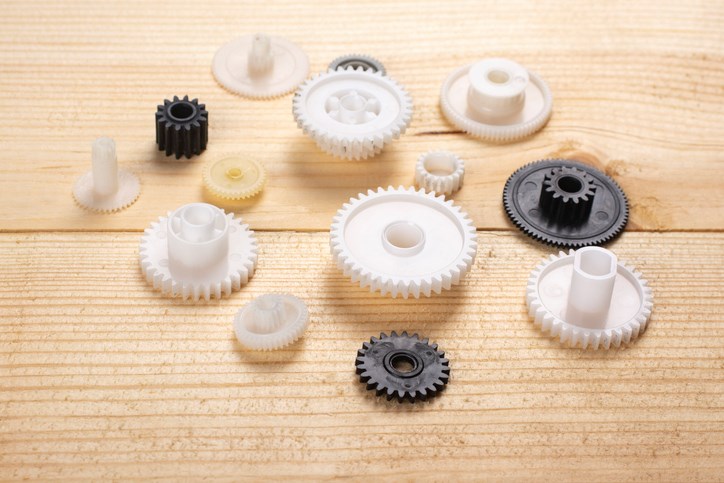
Injection molded products are everywhere. Medical devices, automotive systems, and consumer goods all rely on precision-molded plastic components. And while most people focus on the production phase, the lifecycle of an injection molded product extends far beyond the manufacturing floor. Understanding the full scope — from design and material selection to production and end-of-life recycling — helps manufacturers make more informed decisions that enhance the durability and sustainability of their parts.
Let’s take a closer look at the complete lifecycle of injection molded products, including the key stages that impact part performance and cost-effectiveness. With these insights, you’ll have the knowledge you need to optimize every phase of the process.
Design and Engineering: Setting the Foundation for Success for Injection Molded Products
The lifecycle of injection molded products begins long before production. In fact, it begins with the very concept of the part. The design and engineering phase provides the first opportunity for optimization. When done correctly, this can help ensure efficient manufacturing, cost-effectiveness, and long-term product performance. Some key factors in this phase include:
- Design for manufacturability (DFM): Applying DFM principles helps streamline production and reduce cycle times by optimizing part geometry, wall thickness, draft angles, and gating.
- Material selection: Choosing the right plastic is critical to functionality and sustainability. Factors like impact resistance, chemical compatibility, temperature tolerance, and recyclability all play a role in material selection.
- Engineering for cost and performance: Thoughtful engineering helps balance cost and quality by selecting materials and mold designs that maximize efficiency, minimize waste, and extend the lifespan of both the mold and the final product.
By prioritizing smart design and engineering, manufacturers can create high-quality, long-lasting injection molded products while improving efficiency and reducing costs.
Precision Manufacturing: The Injection Molding Process
During injection molding production, every step is critical to ensuring high quality and consistency. The right combination of tooling, material processing, and automation plays a key role. High-quality molds, for instance, ensure tight tolerances and uniformity and reduce defects, which translates to faster production times and lower overall costs. Proper tool setup further optimizes production efficiency, ensuring minimal downtime and precise part replication.
Consistent material processing is also essential for repeatability and zero-defect manufacturing. Temperature control, pressure settings, and injection speeds must be finely tuned to meet product specifications and tight tolerances.
Automation is vital to speed, precision, and quality control. At Thogus, we integrate advanced robotics and in-process monitoring to enhance efficiency. With automated systems, each part undergoes rigorous quality checks during production, ensuring consistent results with minimal manual intervention. Additionally, data-driven quality monitoring helps detect issues early, minimizing defects and improving overall production output.
Post-Molding Operations and Product Use
Once the injection molding process is complete, post-molding operations ensure that the product meets its final specifications and functions as intended in its real-world application. Secondary operations such as annealing, painting, ultrasonic welding, and assembly are used to optimize the final product.
Beyond that, ensuring that injection molded products perform as expected over their entire lifecycle is crucial for manufacturers and end users. Properly engineered parts and effective post-molding operations can ensure longevity and reliability even in harsh environments.
Sustainability and Recycling in Injection Molding
As sustainability becomes a growing priority across industries, injection molders are turning to greener practices while maintaining performance. There are multiple ways that injection molders reduce environmental impact:
- Smarter material choices: Using recyclable resins like PET, PP, and HDPE or switching to bio-based options like PLA and PHA helps lower carbon emissions and supports more sustainable end-of-life outcomes for molded parts.
- Recycling at end of life: Mechanical recycling — or shredding and reprocessing plastic waste — is widely used for thermoplastics. For harder-to-recycle plastics, chemical recycling is gaining traction by breaking materials down to their base monomers, enabling true closed-loop reuse.
- Circular manufacturing practices: Circular strategies like reusing regrind (cleaned scrap plastic) and closed-loop systems help reduce raw material use and cut down on waste. These methods support both cost efficiency and environmental goals, aligning with rising consumer and regulatory expectations.
By embracing recyclable materials, advanced recycling techniques, and circular production models, injection molders can lead the way in sustainable manufacturing.
Partnering with a Forward-Thinking Injection Molder
At Thogus, we understand that the future of manufacturing lies in delivering products that are not only high-performing but also environmentally responsible. By choosing to partner with us, you gain access to expert material selection, advanced engineering support, and optimized production processes — all designed with sustainability at the forefront.
Our engineers ensure that every product we manufacture is designed with long-term performance in mind, and we apply sustainable practices across every stage of production. Whether you're developing products for automotive, medical, consumer goods, or industrial markets, we help integrate recyclable and bio-based materials into your designs, helping you meet both performance and sustainability goals.
With our process optimization capabilities, we ensure that our injection molding operations are efficient and environmentally responsible. From minimizing waste through circular manufacturing to enhancing recyclability, we prioritize sustainability without compromising product quality or functionality.
Contact us today to learn more about how we can help you create environmentally responsible products without sacrificing quality.
Experience the Thogus Difference
Connect with us today to discuss your project and to learn more about our capabilities.