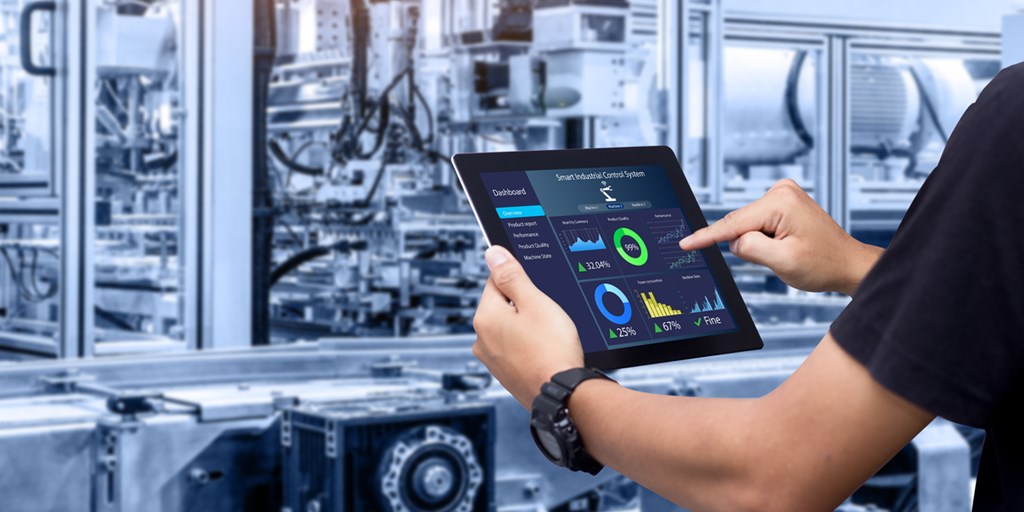
What is Root Cause Analysis?
Root Cause Analysis (RCA) is the process of finding the source from which a problem derives (its “root cause”) in order to identify solutions that treat the problem at its origin. The use of RCA is based on the understanding that it is better to fix problems at the systemic level by looking for underlying issues than it is to deal with problems on a case-by-case basis.
For that reason, RCA has three goals:
- To discover the root cause of a problem
- To fix or address that root issue
- To learn from these results to prevent future problems
RCA is a flexible methodology that should be adapted to meet the needs of your own unique company and situation, not a one-size-fits-all approach. In fact, because RCA is designed to identify the origins of problems that may begin within many different systems, there are many different tools and processes that can be used equally well to accomplish RCA.
Why Use Root Cause Analysis?
RCA advocates for treating the underlying disease, not the symptom. When symptoms alone are treated, the fix is temporary and the problem is likely to resurface, either in the same way or perhaps even more severely. Even more worrisome, underlying systemic issues can cause new problems to arise when and where you least expect them, creating further delays as well as quality and productivity issues.
Steps to Complete Root Cause Analysis
While there are many different methods that might make up a root cause analysis, all of them require the same six basic steps:
- Define the Problem: Whether the problem is with productivity, manufacturing quality, safety, or any number of other potential areas, the first step is always to make sure you understand exactly what you’re trying to fix. Was there a specific incident that prompted this investigation, or maybe just a series of daily habits that you noticed aren’t up to par?
- Gather Information, Data, and Evidence: Remember, this is a systematic analysis — you don’t want to rely on your gut or initial perceptions of what might have happened, as that will only lead you to surface-level conclusions. Instead, carefully collect all the information you can, focusing on verifiable facts and quantifiable data.
- Identify all Contributing Issues and Events: Using your data and evidence, find out everything you can about all parts of your operation that are related to the initial problem. Remember, with RCA, you’re looking at the whole system for flaws; you can’t see those flaws without first understanding the connections between all the nodes in the system.
- Determine Root Causes: Once you understand the system and everything that contributed to your initial problem, you’re ready to determine the root cause — the disease that produced all the symptoms. Keep in mind that there may be multiple, overlapping root causes for a single problem or family of problems. If that’s the case, they’ll all need to be addressed.
- Make Recommendations for Solving the Root Problem, or Mitigating its Effects: Once the problem is defined, you can begin making suggestions for how to solve it. Remember, suggestions should address the most important impacts of the central problem. While it may not be possible to eliminate the problem altogether, you can always soften its impact or prevent it from occurring again in the future.
- Implement the Solutions: The last step is the follow-through; after making your recommendations and evaluating them thoroughly in context, you’re ready to put the best option into action.
Implementing RCA at Your Business
Your business might use many different RCA methods at different times, depending on what problems arise and the context in which you need to solve them. Here are some common RCA methods to have in your tool belt:
- Pareto Charts: a line graph combined with a bar chart that helps illustrate both the frequency and the relative significance of factors that contribute to your main problem
- 5-Whys: the process of continually asking “why?” until you are able to arrive at the root cause of the problem
- Fishbone Diagram: sorts causes and effects into an easily traceable pattern for simple analysis
- Failure Modes Effects Analysis (FMEA): the step-by-step analysis of all possible points of failure in a design or process as well as the possible effects of that failure
With these options and many others available, the most crucial component of successfully implementing RCA in your business is ensuring that the members of your staff responsible for quality and efficiency control have a detailed understanding of all parts of the manufacturing process, and that they are trained in the critical thinking skills necessary to choose the best RCA method(s) for any situation that arises.
Thogus believes in working with clients as true manufacturing partners. For any project we are involved with, we focus on manufacturing by design to make sure that we understand the ins-and-outs of the entire manufacturing process so that we can help solve problems starting at their roots.
Experience the Thogus Difference
Connect with us today to discuss your project and to learn more about our capabilities.