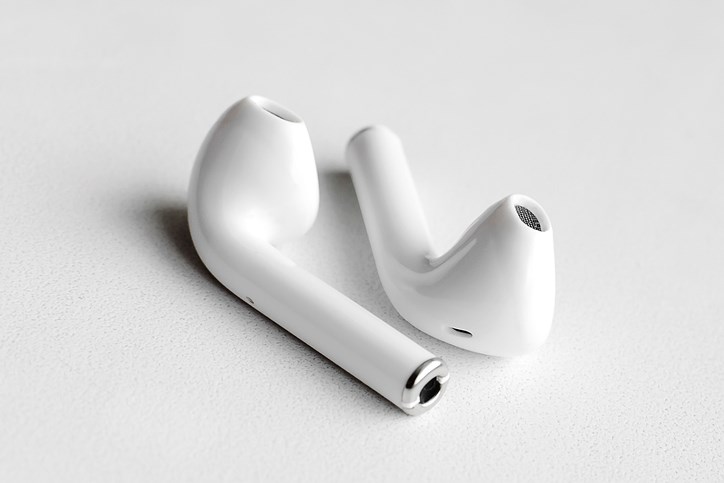
When it comes to electronics, most people probably think of metal manufacturing as the primary method involved. And while that’s true for certain components, plastic manufacturing is essential for parts like plastic enclosures for electronics. Electronic enclosures are critical for extending the lifespan and overall performance of the application. EMI/RFI shielding and heat dissipation are just two of the protections that plastic enclosures provide for electronics.
Injection molding is the most commonly chosen method for producing these enclosures due to its versatility and precision. Below is a look inside the process of injection molding plastic enclosures for electronics.
An Overview of the Production Process
The manufacturing of plastic enclosures for electronics involves several key phases. They each contribute to the overall quality and functionality of the final product. In general, the process usually looks something like the following:
- Design Phase—This involves identifying the design specifications and functional requirements, and creating a 3D design of the enclosure with CAD software. Engineers will consider factors such as size, shape, internal layout, mounting options, and any additional features like display windows or openings for connectors.
- Material Selection—Manufacturers will choose suitable materials based on the requirements of the application by considering factors like mechanical properties, chemical resistance, UV resistance, and cost. This is also when your manufacturing partner will ensure materials meet regulatory and environmental standards.
- Tooling and Mold Design—Once materials are selected and the 3D design is finalized, engineers will develop the mold and design it to accommodate the geometry of the enclosure. Mold design will also be optimized for efficiency and cost-effectiveness.
- Injection Molding Process—The actual production of the plastic enclosure involves setting up the injection molding machine with the appropriate parameters, feeding the resin pellets into the machine’s hopper where they are melted and injected into the mold, and releasing the enclosure after the part has cooled.
- Post-Processing—Depending on the application, the part might require additional processes and handling after molding, such as heat-staking, pad printing, painting/coating, etc..
- Assembly and Packaging—If your injection molder offers it, this is when assembly and packaging takes place. Assembly may involve adding components like gaskets, fasteners, or connectors. This is a good time to verify the fit and functionality of the product. And then the product will be packaged according to customer specifications.
Why Choose Injection Molding for Plastic Enclosures for Electronics?
Injection molding is often considered the best method for producing plastic enclosures for electronics. Its versatility and precision make it well-suited for high-volume manufacturing of highly detailed and complex parts with tight tolerances. This is crucial for ensuring electronic components fit securely within the enclosure and meet design specifications.
For manufacturing enclosures in large quantities, injection molding is also one of the most cost-effective options. Once the mold is created in injection molding, the cost-per-part decreases as the production volume increases. Not only does this allow for mass production within a manageable budget, but it also opens the door for scalability and flexibility.
Some Things to Consider
There are a few things to consider when it comes to choosing injection molding for the production of plastic enclosures for electronics.
First, the initial tooling cost of injection molding can be higher than other manufacturing options. Tooling cost is often influenced by a variety of factors, including part complexity, mold size, tolerance and precision requirements, and surface finish requirements. However, keep in mind that this initial cost is typically offset during high-volume production runs.
Second, lead times can vary with injection molding based on the time it takes to design and create the molds. However, once production begins, cycle times are usually much faster than most other methods.
Thogus Offers High-Volume Injection Molding Solutions for the Electronics Industry
At Thogus, we provide end-to-end injection molding solutions for customers in a wide range of industries, including the electronics industry. We specialize in providing high-volume production for both standard and customized parts. Our approach to injection molding hinges on full collaboration and transparency so you can be sure you’re getting exactly what you need.
If you’re looking for a supplier with knowledge of the electronics industry, reach out to our team today to get started.
Experience the Thogus Difference
Connect with us today to discuss your project and to learn more about our capabilities.