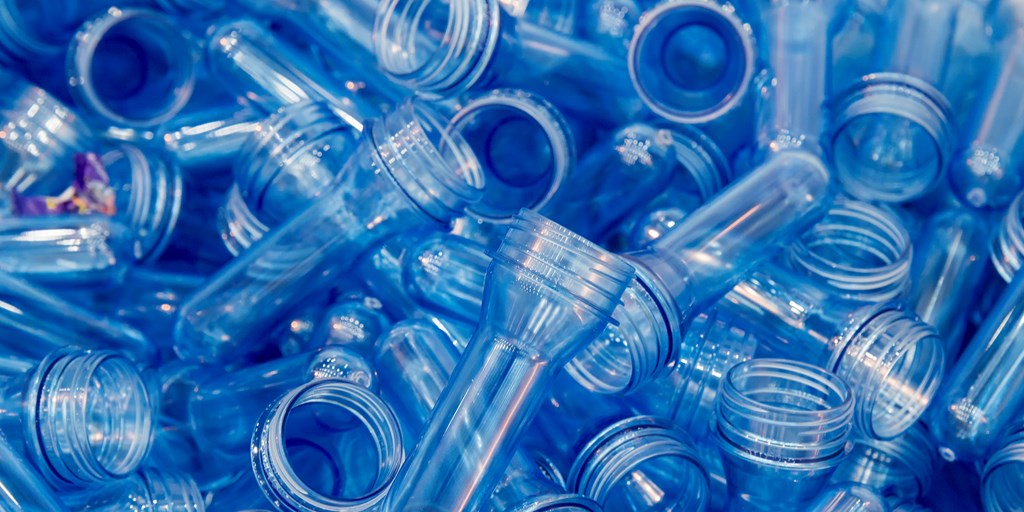
Plastic injection molding can be an ideal method for a variety of parts and projects. From medical devices to automotive and industrial parts, to pieces for small household appliances, plastic injection tools can be designed to meet any specifications you can imagine and has the added benefit of faster production times and more lightweight and cost-efficient final products.
Step one in an efficient project is to get the part design right early in the process to avoid costly delays. Greg Werner, the Thogus Application Development Engineer and overall tooling guru, recommends keeping the following considerations top-of-mind when designing a new injection molded part.
Draft
The draft is the angle or taper on the surfaces of a molded part that moves across tool steel of the mold as the part is coming out of the mold. Including this angle in your part design from the beginning saves on costs and makes the part easier to demold, because it reduces the amount of pressure required by the demolding process. Usually, you want to have a minimum of one degree draft per wall. Adding a draft can complicate the design process, but it’s well worth the extra effort, as parts with no draft can be warped or scratched during the ejection process.
Internal Undercuts
An undercut is any feature of an injection-molded part that prevents it from easily sliding out of the mold — think crevices and holes, protrusions, or threaded pieces. In general, undercuts can be challenging to manufacture. But undercuts on internal diameters and features should be avoided if at all possible.
Internal undercuts require more complicated adjustments, such as collapsible cores that still have some room for engineering improvement. External undercuts, on the other hand, are easier to account for with some solutions as simple as adjusting the parting lines on the mold. If you absolutely must have internal undercuts in your part, try to keep the features as small as possible, and consult with your toolmaker to ensure that the tool is up to the job.
Tolerances
Tolerances help bridge the gap between the idea of a design and the reality of a part — they define what is allowable in terms of deviation from specifications. Because they’re focused on acceptable standards, it’s helpful to include both allowable positive and negative deviations around nominal values. Tolerances for all parts and processes are not equal; you can’t apply metal machining tolerances to an injection molded part. In order to determine your tolerances, it’s important to have a good understanding of best practices for the material, part size, and injection molding process you are working with.
Wall Thickness
The important thing to focus on is keeping the wall thickness as uniform as possible in your design, and following the material and part design guidelines when adding features like ribs to minimize sink. It’s also best to avoid thick to thin transitions, as these can create bottlenecks that slow down the injection process and weaken parts.
Threads
Many parts require threads, which creates challenges in the injection molding process and requires a lot of thought to create a functional design. First, make sure that you’ve accounted for proper draft to avoid damaging your part during the production process. Then, think about the overall look and function of your threads — you want them as large as possible for the application to avoid unnecessary wear and tear, and uniform from start points to stop points, rather than thinned out to create a sharp end. The pitch, or distance between the threads, is also important, as threads with small pitch tend to strip more easily, especially with plastic parts.
Ready to start designing? Schedule a phone consultation to get expert engineering support.
Experience the Thogus Difference
Connect with us today to discuss your project and to learn more about our capabilities.