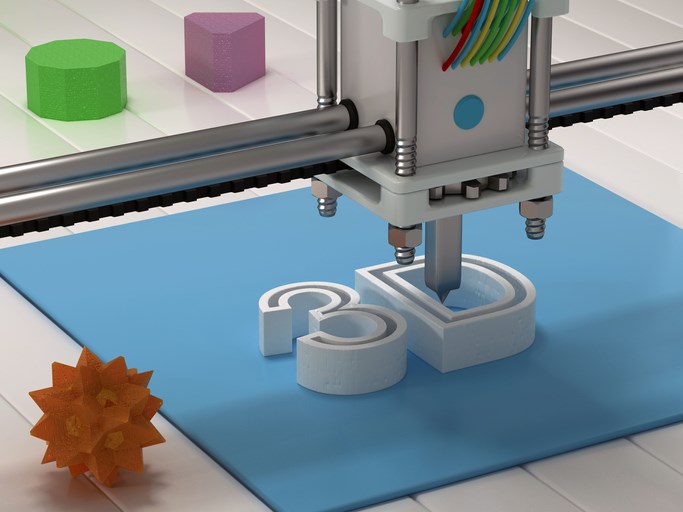
Ever since 3D printing entered the plastic manufacturing scene in the 1980s (much earlier than most people think), it has been rife with potential. In recent years, more sophisticated technology has allowed that potential to be fully realized. But it does put an important decision in the hands of product designers and engineers: is 3D printing or injection molding (an even older process) the right choice for your products? Both processes have notable advantages and drawbacks, but performing a cost analysis of 3D printing vs. injection molding is a good place to start.
A Brief Overview of 3D Printing and Injection Molding
3D printing, also called additive manufacturing, is a process that creates 3D objects by adding material layer by layer based on a digital model (usually CAD). Thermoplastics, high-performance resins, and consumer plastics all work well with 3D printing, making it a versatile process with a wide range of applications. While slower than some other processes and more expensive for large-scale runs, 3D printing is an excellent solution for rapid prototyping, parts with complex geometries, low waste, and on-demand production.
In contrast, injection molding is a process that injects molten material into a mold. Compatible with a wider range of materials, including thermoplastics, high-performance resins, and thermosetting plastics, injection molding has been the go-to for industries that benefit from high-volume production, speed, precision and consistency, and design freedom. However, injection molding does come with additional tooling costs, size constraints, and prototyping limitations.
The Cost Analysis: 3D Printing vs. Injection Molding
There are a lot of factors that go into a cost analysis of 3D printing vs. injection molding. Because every project is unique, it’s not possible to provide a fully comprehensive breakdown, but the following comparison should provide a workable foundation for understanding the differences between the two.
Cost Factors in 3D Printing
Materials—Material costs vary depending on the type and quality. Common materials like PLA are going to run much cheaper than specialized engineering-grade resins. There are also consumables like build platform adhesives, support materials, and cleaning solutions that may contribute to the cost.
Equipment and Maintenance—The upfront investment for an industrial-grade 3D printer can run tens of thousands of dollars, so you should expect that to factor into production costs. The printing machines also require regular upkeep including cleaning, calibrating, and replacing worn-down parts like nozzles or build surfaces. It’s also a good idea to factor in energy consumption here. The energy required to support a run depends on the printer type, process duration, and heating elements.
Labor—Labor costs are associated with everything from the initial design work and support structure generation to monitoring and post-processing. While the actual 3D printing process is mostly automated, skilled laborers are still needed to optimize designs, load materials, monitor the process for issues, and necessary post-processing clean-up. If parts require extensive post-processing, this can get costly.
Other Costs—3D printing comes with an assortment of other associated costs, including overhead for space, utilities, and certifications; printer depreciation; material waste; and 3D printing software and licensing.
Cost Factors in Injection Molding
Materials—Like 3D printing, the cost of materials will vary depending on the amount and type of resin. Additives like colorants, UV stabilizers, flame retardants, or reinforcing agents may also be required for certain parts.
Equipment and Maintenance—Compared to 3D printing, injection molding requires more in terms of the equipment required. You’ll need to factor in the cost of the mold (design, machining, and tooling), which can vary based on the complexity of the part, as well as the upfront cost of the injection molding machine. As far as maintenance goes, injection molding machines also require regular upkeep and part replacement and the energy required to heat the resins can be significant.
Labor—Injection molding is typically a more involved process than 3D printing. It requires skilled laborers for the initial set-up and tooling adjustments, running the machine, monitoring the process, and ensuring product quality. Inspection and quality control personnel may also be needed to ensure the parts meet the customers’ demands.
Other Costs—Like 3D printing, injection molding also comes with a variety of other associated costs such as overhead for manufacturing facilities, insurance, and certifications; mold depreciation; recycle costs associated with material waste and scrap; and post-processing and tooling maintenance.
Comparative Cost Analysis of 3D Printing vs. Injection Molding for Short Runs
In a cost analysis of 3D printing vs. injection molding for short runs, two major considerations are the per-part cost and the time to market. The per-part cost involves several factors like materials, equipment, labor, and overhead (see above). But time-to-market is slightly more complicated. Here is how the two processes compare:
3D Printing: 3D printing is ideal for rapid prototyping, allowing for quick iterations of design and faster time-to-market. With 3D printing, short runs can be produced on demand, which reduces the lead time associated with traditional manufacturing methods. 3D printing also eliminates the need for tooling and allows for much greater flexibility in design. However, 3D printing is generally a slower process and often has a higher per-part material cost.
Injection Molding: Thanks to the need for specialized tooling and mold production, the time-to-market for injection molding can be noticeably longer than that of 3D printing. However, the overall process is much quicker, cutting down the time of production.
The Take-Away: For shorter runs with limited quantities, 3D printing is often the more cost-effective option due to the lower upfront tooling costs and faster time-to-market.
Comparative Cost Analysis of 3D Printing vs. Injection Molding for Long Runs
Here is how 3D printing and injection molding compare for long production runs:
3D Printing: The benefit of 3D printing for long runs lies in its design flexibility and adaptability. However, 3D printing is generally slower than injection molding, which lengthens the time-to-market, particularly when production requires parts in the thousands or more.
Injection Molding: In contrast, the upfront time investment in tooling for injection molding is often offset by the efficiency of the process. Once the mold is ready, injection molding can produce a large number of parts relatively quickly, without variation in part quality and consistency.
The Takeaway: For production runs in the thousands of parts or more, injection molding is by far the more cost-effective option due to its efficiency and lower per-part cost.
3D Printing vs. Injection Molding: Which is Right for Your Project?
So which one is right for your product? Ultimately, a cost analysis for 3D printing vs. injection molding should be tailored to specific project requirements, including part quality requirements, design constraints, lead time considerations, and budget concerns.
But in general, if you need a lower volume of parts and could benefit from unmatched design freedom, 3D printing is the more cost-effective option.cost analysis 3D printing vs injection molding
However, if you need parts in the thousands and your part can be optimized for manufacturing, injection molding is the better choice.
Contact Thogus for a More Thorough Cost Analysis of 3D Printing vs. Injection Molding
At Thogus, we specialize in offering mid- to high-volume injection molding services for a range of industries, including medical, consumer goods, electronics, industrial, plumbing, and automotive. With a commitment to staying at the forefront of the manufacturing industry, we approach every project with a focus on customizing our processes to meet the needs of our customers.
Are you looking for an injection molding partner that has the expertise to handle your project? Connect with us today to get started.
Experience the Thogus Difference
Connect with us today to discuss your project and to learn more about our capabilities.