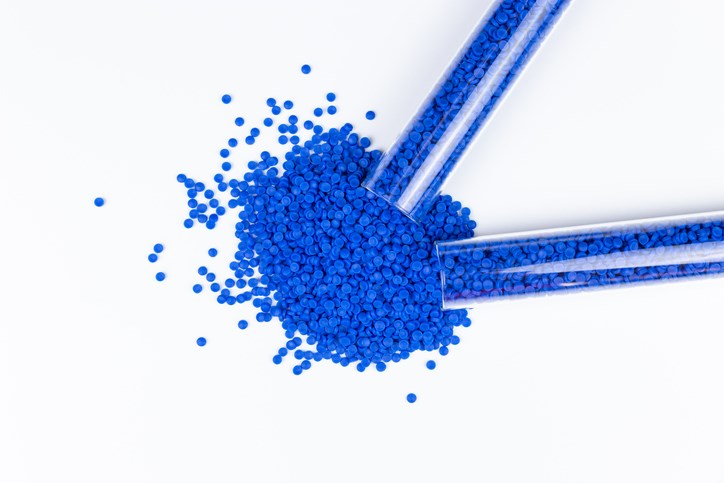
From creating intricate components for the automotive industry to producing life-saving medical devices, injection molding plays a vital role in shaping the modern world. It’s a highly repeatable process that can deliver high-volume manufacturing solutions without compromising on part quality or precision.
And, like most other manufacturing methods, injection molding has seen its fair share of innovation that has allowed it to reach new levels of capacity and versatility. One such example is injection molding additive manufacturing.
In the case of injection molding, additive manufacturing refers to the use of fillers that are added to the thermoplastic in order to enhance or add certain properties. Because there is such a wide selection of combinations and options, injection molding manufacturers offer invaluable services for tailoring solutions to diverse industries through the use of additives.
The Power of Injection Molding Additive Manufacturing
As discussed above, the benefits of injection molding additive manufacturing are wide and varied and include:
- Increased material strength — One of the most notable advantages of additive manufacturing is the ability to enhance the strength of the base material. Reinforcing glass fillers, for example, adds multi-directional rigidity to parts because the thin fibers will harden at different angles within the finished product.
- Improved thermal properties — In applications like those found in automotive or aircraft engines, a part must be able to withstand extremely high temperatures on a regular basis and for long periods of time. In this case, filler material like ceramic can be used to improve the thermal performance of base polymers.
- Better durability — Parts that can stand up to constant strain are essential in industrial applications. Not only do they ensure the continued performance of heavy-duty equipment and machinery, but they also meet the safety standards often required by these applications. With materials like toughened thermal fillers, manufactured components are much more resilient to wear and tear.
- Customized solutions — Another one of the most notable benefits of injection molding additive manufacturing is the ability to tailor materials and components to the specific needs of an application. Whether producing biocompatible medical devices with bioactive fillers or crafting lightweight automotive parts using advanced composite fillers, additives in injection molding enable manufacturers to produce parts based on the customer’s requirements.
Types of Fillers and Their Applications
Now that we have a basic understanding of what fillers can do, what are the options? Different types of fillers exhibit different properties that make them ideal for certain applications and not well-suited for others. While there is a long list of different types, fillers can be broadly classified as glass, ceramic, thermal, colorants, and flame retardants.
Glass fillers are typically made from glass particles or fibers. Injection molding manufacturers often use glass when they want to enhance the dimensional stability of a component. Ceramic and thermal fillers, on the other hand, are excellent solutions for parts that need additional heat resistance and heat conductivity, while flame retardant fillers reduce the flammability of a material.
On the aesthetic side of things, colorants come in powders, pellets, and liquids and, when added to materials, can help manufacturers achieve a certain color.
Industry-Specific Applications
With nearly limitless versatility, fillers make it possible for injection molding manufacturers to produce parts for highly specialized purposes in a wide array of industries, including:
- Healthcare — Biocompatible materials are used for medical devices that must comply with strict regulatory standards.
- Consumer products — Fillers reinforce products to ensure longevity and reliability, while also adding attractive colors that customers enjoy.
- Plumbing — High-performance materials with enhanced corrosion resistance prolong the lifespan of plumbing components.
- Electronics — Enhanced thermal conductivity for more efficient heat dissipation is critical to the performance of electronic components.
- Industrial — Toughened materials for heavy-duty components that can withstand rigorous industrial applications.
- Automotive — Lightweight materials with enhanced mechanical properties deliver better fuel efficiency without sacrificing safety.
- Precision Engineering in Injection Molding Additive Manufacturing
Injection molding additive manufacturing is not a one-size-fits-all solution. Injection molding experts should work closely with clients to tailor filler combinations that meet specific requirements.
Selecting the right materials is critical. An injection molding partner can help you consider important factors like mechanical and chemical properties, environmental resilience, and regulatory compliance.
In order to ensure the materials meet expectations, manufacturers can conduct thorough testing and share results with customers to ensure client-centric solutions.
Choose an Expert in Injection Molding Additive Manufacturing
At Thogus, we’ve been providing medium- to high-volume injection molding manufacturing solutions for more than 70 years. Our 76,000 sq. ft. facility is equipped with 35+ state-of-the-art injection molding machines that range in tonnage from 35 to 720 tons.
With our commitment to white glove service and collaboration, we aim to provide meticulously tailored plastic injection molding solutions that meet the unique needs of each of our customers. At Thogus, we’re about more than just manufacturing a part and calling it a day. We’re here to be your contract manufacturing partner from start to finish.
Looking to get started? Connect with our team today.
Experience the Thogus Difference
Connect with us today to discuss your project and to learn more about our capabilities.